原子力システム 研究開発事業 成果報告会資料集
レーザー加工技術の組み合わせによるFBR熱交換器伝熱管内壁検査技術の高度化に関する技術開発
(研究代表者)西村昭彦 量子ビーム応用研究部門
1.研究開発の背景とねらい
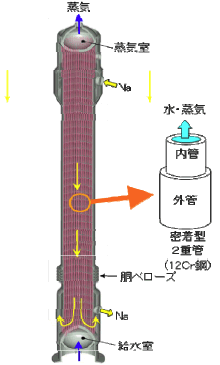
図1 次世代FBR熱交換器
本事業では次世代ナトリウム冷却型FBRにおける蒸気発生器のための検査補修技術の高度化のために、内壁面に生じる微小欠陥等を早期発見し、その場での補修を可能とする新プローブの開発を目的とする。
本課題の背景として、FBRに関して、熱交換器内で共存するナトリウムと水の化学反応に対する長年の危惧がある。一方でレーザー加工技術に関するものとしては、超短パルスレーザー加工の著しい進展により、新たな応用分野としてFBRの熱交換器伝熱管の補修技術の開発が可能となった。現在のFBR原型炉であるもんじゅの熱交換器はヘリカル型の蒸発器と過熱器を組み合わせた構造であり、蒸発器の伝熱管内には高温水と蒸気が混相流として流れ、外側を液体ナトリウムが流れる。また、これまで設計と要素技術開発が進んでいる次世代FBRの熱交換器は2重管構造による直管型の大型熱交換器が提案されている。いずれにしても、これまでは渦電流探傷(ECT)による検査により伝熱管に欠陥が発見された場合、伝熱管を施栓により塞ぐのが対処の基本である。しかしながら施栓の割合が高くなると有効伝熱面積の減少となり、結局は熱交換器の寿命を縮めることとなる。現在、ECTの検出性能の向上とともに伝熱管内壁の微細な欠陥の発見が可能となりつつあり、発見した微細な欠陥を補修することで施栓を回避することが望まれる。本プロジェクトでは、伝熱管を検査だけでなく欠陥の発見に併せてその場での補修を試みる新型プローブを開発する。これに必要な経験がITER核融合ブランケットの枝管をレーザー溶接・切断するロボット装置として、1999年に複合光ファイバを用いたレーザー熱加工による補修である。ITERプロジェクトでの開発終了後、この複合光ファイバは光ファイバ内視鏡とレーザーメスの融合技術として積極的な医療応用が進められている。
以上のように本課題には、もんじゅの後継にあたる次世代FBRの熱交換器伝熱管の検査補修技術の推進として、レーザー技術、原子力、医療という離れた分野間の連携によって新技術のブレイクスルーを生じさせることがねらいとして含まれている。
2.研究開発成果
2.1 概要
開発するシステムは、次世代FBR熱交換器の伝熱管を検査補修するための新型プローブシステムであり、ECT検査技術、複合型光ファイバ技術、レーザー熱加工および超短パルスレーザー加工技術を統合させ、従来の検査機能に補修・保全機能を備えている。
これまでに主要技術の整備は順調に進展し、開発した要素部分の統合を進めることが出来た。要素部分は、伝熱管内壁の映像を伝送する画像用光ファイバと欠陥部位のレーザー熱加工溶接による補修のためのエネルギー伝送用光ファイバを同軸構造に組み合わせた複合型光ファイバである。レーザーとしては小型高性能化が著しいイッテルビウムファイバレーザーを採用した。複合型光ファイバの周りには照明用のライトガイドを設けた。このファイバの先端には伝熱管の内壁の撮影と加工補修のためのレーザー加工ヘッドを接続した。レーザー加工ヘッド内には伝熱管内壁を360度スキャンし、レーザー照射位置を微調整するための小型ステッピングモーターを内蔵した。また、複合型光ファイバの反対側の端面では、画像とレーザー光の分離のためのカップリング装置を製作した。さらにレーザー加工ヘッド直近には複合型光ファイバを抱え込む形でECT用マルチコイルセンサを設けた。
2.2 ECTセンサヘッド用ソフトウエアの開発
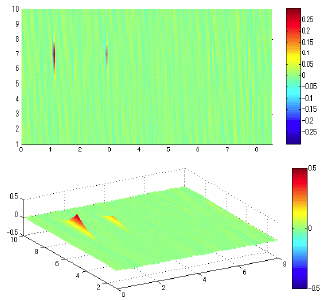
図1 欠陥測定結果と立体表示
周方向ノッチ W0.3×L10
50%深さ(図中左)、20%深さ(図中右)
ECTに関する統合については、先ず、直管型熱交換器の模擬伝熱管の内径の精密測定と複合型光ファイバスコープの外径の精密測定を行い、ECT中空センサユニットの中空部の寸法改良を実施した結果、複合型光ファイバスコープと組み合わせを確実にした。次に、ECT用探傷器の信号ケーブルと複合型光ファイバスコープの組み合わせを検討し、両者を熱収縮チューブにて一体化することで統合を終了した。模擬伝熱管補修試験で使用する模擬伝熱管には、内壁に模擬欠陥を施した。ECT中空センサユニットを模擬伝熱管内に挿入し、渦電流の変化量を測定して欠陥の有無を評価した。測定にて得られたアナログ信号をデジタル化し、フィルタリング処理を施すことで欠陥識別の妨げとなる雑音成分を除去し、欠陥を視覚的に理解しやすいように立体表示が可能なソフトウエア開発を行った。このソフトウエアの開発によりプロトタイプのECT探傷器の製作を終了した。図1に微小欠陥の測定結果と立体表示を示す。
平成20年度、プロトタイプECT用探傷器として複合型光ファイバスコープの組み合わせを実施したことで、次年度の模擬伝熱管補修試験に先立って伝熱管内へのプローブ挿入試験が可能となった。加えて、次世代FBR熱交換器として検討が進められている内径1/2インチ配管への対応においては、信号線の減数化のためのマルチプレクサの製作が必要である等、模擬伝熱管補修試験に向けての問題点を明らかにし、マルチプレクサの開発を計画した。
2.3 レーザー加工ヘッド用ソフトウエアの製作
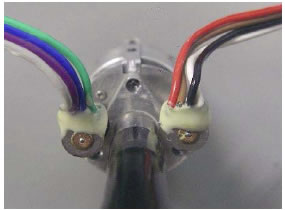
図2 レーザー加工ヘッドと複合型ファイバスコープの接合部分
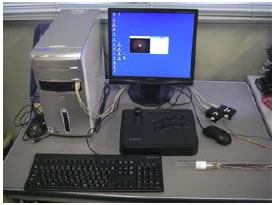
図3 完成した制御システム
平成19年度に製作したレーザー加工ヘッドと複合型光ファイバスコープを統合した。統合したシステムを用いて模擬伝熱管補修試験にて用いる模擬伝熱管内にてレーザー加工ヘッドを動作させて、管内壁の欠陥を撮影し、トレースするためのソフトウエアを開発し、プロトタイプのレーザー加工ヘッド制御装置を製作した。
レーザー加工ヘッドと複合型光ファイバスコープの統合に関して、機械的にはファイバスコープ部分のステンレス管にレーザー加工ヘッド取り付けのための金具を取り付け、レーザー加工ヘッド側に設けた3箇所のネジ穴とをボルトで結合させた。図2にレーザー加工ヘッドと複合方ファイバスコープの接合部分を示す。また、光学的にはレーザー加工ヘッドの可動スリーブ先端に内蔵したミラーからの映像をファイバスコープで取り込むと共にファイバスコープ外周部分に設けたライトガイドにより対象を照明できることを確認した。統合したシステムを用いたレーザー加工ヘッドの動作については、直線動作と回転動作を独立して行い、伝熱管内壁に対して接触等による動作不良の生じないことを確認した。管内壁の欠陥を模したテストパターン紙の撮影像の取得を行い、ソフトウエアによりこの撮影パターン上を手動で追従させた。こうした動作履歴を記録し再現できることを確認した。製作したプロトタイプのレーザー加工ヘッド制御装置には、開発したソフトウエアのインストールを行った。図3にソフトウエアをインストールした制御システムを示す。
平成21年度は、開発したソフトウエアの改良点として、撮影画像の記録や手動操作の記録機能の追加を行う。さらに、伝熱管内壁の溶接補修のためのイッテルビウムファイバレーザー光の出力やレーザー照射時間の制御及びレーザー照射による伝熱管内壁の温度上昇の数値シミュレーションによる予測等の機能追加を行う。
2.4 カップリング装置の製作
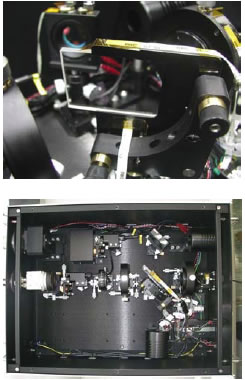
図4 カップリング装置
ダイクロイックミラー(上)
カップリング装置内部全体(下)
カップリング装置の製作にあたり、レーザービームの出力、波長、広がり角を設計基準としたIPGフォトニクス社のイッテルビウムファイバーレーザーとの接続部はQBHコネクターとした。このレーザーと伝熱管内壁からの映像との統合・分離を行うためのダイクロイックミラーには、温度上昇を監視できるようにマウントに熱電対を取り付けた。レーザー光を1で製作した複合型光ファイバスコープの接続部端面に導くため、レーザー光を平行光にするためのコリメーターを製作した。また、本レーザー装置は加工のためのレーザー波長と集光位置調整のための内蔵ガイド光レーザーの波長が異なるため、この波長の違いにより焦点位置が異なる色収差現象を補正する補正光学系を設けた。また、集光位置をカップリング装置の外部から微調整できる機構を設けた。複合型光ファイバスコープからの映像はダイクロイックミラーを通過し、CCDカメラ上に結像する配置とした。以上の基本設計を基に各光学部品配置を組み立てにカップリング装置を完成させた。図4にカップリング装置内部のダイクロイックミラー部分(上)と内部全体の様子を示す。
複合型光ファイバスコープ、レーザー加工ヘッド、高出力ファイバーレーザー等の各要素が接続されるカップリング装置の製作を行い、基本性能を確認した。伝熱管内壁の映像を撮影するためのCCDカメラの解像度と温度上昇監視のための記録計の仕様等、平成21年度のカップリング装置の完成に必要な機材の仕様を確定した。
2.5 模擬伝熱管補修試験準備
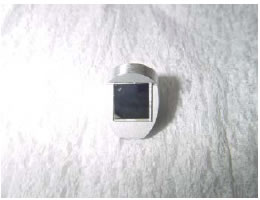
図5 試作に成功した耐熱ミラー
欠陥を内壁に設けた模擬伝熱管を製作し、 これまで製作した装置を用いて、平成21年度の補修試験に向けた予備試験を実施した。予備試験の結果を踏まえ、課題を抽出し、平成21年度に実施する補修試験の試験計画を立案した。
本試験のため欠陥を設けた模擬伝熱管は、もんじゅ蒸発器で使用している低クロム鋼(内径1インチ直管伝熱管)である。これに機械加工及び放電加工により欠陥を導入した。欠陥の方向は、周方向、軸方向、斜め45度の3種類である。複合型光ファイバスコープに10Wのイッテルビウムファイバーレーザー光を入射させたところ、可動スリーブ内の45度に設置した金属ミラーに破損が生じるという第1の課題が明らかとなった。次に、最大1kWのイッテルビウムファイバーレーザーを入射させ、1インチ伝熱管を外部から照射する予備実験を行った。その結果、出力300W以上ではレーザー照射部からの蒸着物により、複合型光ファイバスコープの前面に設けた保護ガラスが汚損することが明らかとなった。仮に、レーザー加工ヘッドを接続し伝熱管の内壁にレーザー照射を行えば、内壁からの蒸着物によりレーザー加工ヘッドの可動スリーブ及び45度に設置したミラーが汚損により使用不能になるという第2の課題も明らかとなった。
これらの2つの課題のうち、第1の課題については、金属ミラーをサファイヤ基板に誘電多層膜を表裏から蒸着させた耐熱ミラーを考案・製作し解決した。図5に試作に成功した耐熱ミラーを示す。また。第2の課題についてはレーザー光を斜め入射させ、伝熱管内を流動する気流を効果的に利用することで、ミラー類の汚損を低減できる目途を得た。これらの結果から、平成21年度に用意するイッテルビウムファイバーレーザーの最高出力は300W以上500W以下が適切であるとの結論を得た。
また、平成21年度の模擬伝熱管補修試験で使用する高速増殖炉研究開発センター敷地内ISI棟の伝熱管モックアップ試験装置については、直管の模擬伝熱管を仮接続できるよう小改造を行い、実験エリアと配電盤の確保を実施した。図6はこのプローブの性能を試験するISI棟もんじゅ熱交換器モックアップ試験設備を示す。以上、試験の実施において解決すべき課題の抽出を行い、試験計画の立案を行った。
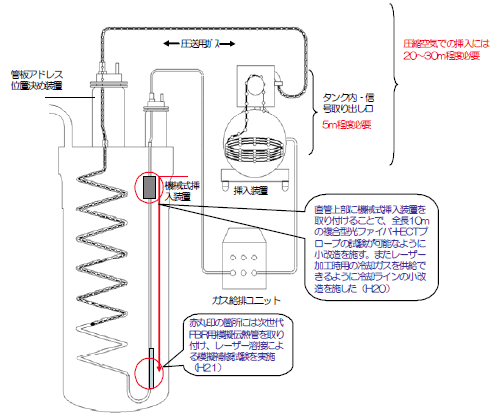
図6 もんじゅ熱交換器モックアップ試験設備の改造
3.今後の展望
平成21年度は、これまで開発した要素技術の統合を行い新型プローブを完成させる。このため、マルチプレクサによるECT信号線の減数化とレーザー加工ヘッド制御ソフトウエアの機能強化を実施する。これらの準備のため、平成21年10月、これまでの開発要素機器を敦賀本部レーザー共同研究所の実験室に運搬し、組み立て作業を実施中である。
4.参考文献
[1] 西村昭彦、峰原英介、塚田隆、"ステンレス鋼表面の超短パルスレーザー光を用いた応力除去法"、特開2005-131704.
[2] 岡潔、エネルギーレビュー、7月号, 2007, pp.7-10.
[3] 科学技術振興機構報第394号, 平成19年4月19日, (http://www.jst.go.jp/pr/info/info394/index.html)