原子力システム 研究開発事業 成果報告会資料集
金属燃料の溶融電解精製における陰極・陽極の処理に関する研究開発
(研究代表者)飯塚政利 原子力技術研究所次世代サイクル領域
(再委託先)国立大学法人 豊橋技術科学大学
1.研究開発の背景とねらい
経済性、安全性、核拡散抵抗性に優れた核燃料サイクル技術が求められる中で、これらの要求を満足する技術の一つとして、U-Pu-Zrなどの合金を燃料とする金属燃料高速炉、溶融塩化物/液体金属溶媒を用いる乾式再処理、簡便な射出鋳造による燃料成型からなる金属燃料サイクル(図1)が注目されている。乾式再処理フローシートの中心となる溶融塩化物浴中における電解精製工程では、せん断された使用済金属燃料を受け取り、ここから核分裂生成元素(以下FP)を取り除き、燃料物質を回収する(図2)。陽極では、各種金属元素の塩化物生成自由エネルギー変化の差を利用して専らZrよりも塩化物生成傾向の強い元素を溶解する。Uは金属製固体陰極の表面に回収し、Puおよびマイナーアクチニドについては、液体Cd中における活量係数が低く還元されやすい性質を利用し、液体Cd陰極にUと共に回収する。固体陰極へのU回収については工学規模試験により実用化に十分な速度が達成できることが確認されている[1]。一方、液体Cd陰極についても、Pu回収に適した条件や希土類FP除染性能などが明らかにされ[2,3]、国外では工学規模での試験も行われている[4]。
しかし、電解精製を使用済燃料からアクチニドを回収してリサイクル燃料原料とし、かつ核分裂生成物を分離廃棄する工程として捉えると、次のような課題が残っている。
(1)陽極残留物処理技術の開発
・電解精製終了後も陽極残留物中に少量残るアクチニド回収プロセスの開発
・SUS被覆管、Zr、貴金属FPからなる陽極残留物を主体とする金属廃棄物処理プロセスの開発
(2)陰極回収物処理技術の開発
・Zrが混入することにより融点が上昇したU回収物のインゴット化(付着塩蒸留除去、U-Zr溶融固化)
・高温の溶融U-Zr合金/塩化物との両立性をもつ蒸留るつぼ材料の開発、および実用機器設計
そこで本事業では、実際にU電解試験で生じた陽極残留物と陰極回収物、および模擬混合物を用いた高温蒸留試験などを通じてこれらの技術開発を実施している。さらに、電解精製工程、陽極残留物/陰極回収物処理工程における技術的な到達度や性能を整合させつつ、U回収率と回収速度を高いレベルで両立するための運転条件を定め、これを基に乾式再処理プロセスにおけるマスバランス、回収率などの性能を評価する。
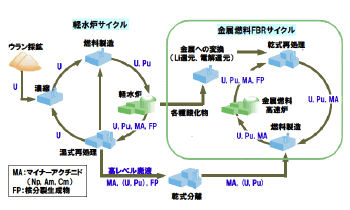
図1 金属燃料サイクルの概念
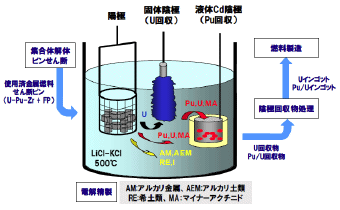
図2 電解精製工程の概念図
2.研究開発成果
2.1 陽極残留物の処理技術開発
2.1.1 U溶解除去後の陽極残留物からの付着塩除去試験
模擬FP(Mo、Pd、Ce、Nd)を含む陽極残留物中に残存する未溶解U金属を除去するために、酸化剤(CdCl2)を加えて溶融塩浴中にUを溶解除去する試験を実施した。陽極残留物中のUがほぼ全量溶解し、酸化反応におけるマスバランスは試験全体を通じて良好であった。溶融塩中濃度の変化などや反応速度などのU、Zrの溶解挙動は、模擬FPを含まない陽極残留物について本事業の中で平成19年度に観察されたものとほぼ同様であった。
平成19年度に実施したU-Zr陽極溶解残留物(模擬FP含まず)からのU溶解除去試験を経た陽極残留物を対象として、後述のU-Zr陰極回収物蒸留試験装置を用いて高温蒸留による付着塩化物除去試験を行った。その結果、電解精製、U溶解除去、高温蒸留という一連のプロセスを通したU残留率が0.047〜0.15%まで低下し、乾式再処理プロセス設計仕様であるU回収率99.5%を考慮しても十分に低い値であることが確認された。また、1400℃までの温度であれば、ZrO2コーティングを施したグラファイトるつぼが適用できることがわかった。
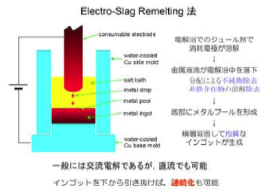
図3 ESR法の概念
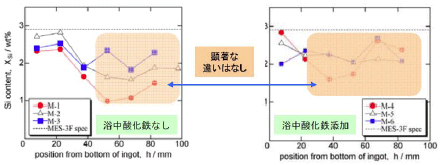
図4 高珪素鋼の再溶解インゴット中珪素分布
2.1.2 陽極残留物からのアクチニド除去工程への高温金属再溶解法の適用性検討
CaF2-20wt%CaO-10wt%Al2O3スラグ中で高珪素鋼(2.91%-Si)を用いたエレクトロスラグ再溶解(ESR−図3)試験を行い、製品インゴット中のSi濃度が原料鋼中の半分程度に低下することを確認した。スラグ中に珪素を留めることを目的に酸化剤(FeO)を加えた効果は見られなかったが(図4 )、短期的には陽極で電気化学的に溶解した珪素に代わってスラグ中のAlが陰極で還元されるためと推測された。また、再溶解電流を上げて原料鋼溶解速度を大きくするにつれて珪素分離効率が低下する傾向が見られた。高い再溶解電流は、電気化学的な珪素溶解速度に対してジュール熱による原料鋼溶融滴下速度の比率が大きくなる条件に相当することから、この結果は珪素除去が上述の電気化学的なメカニズムにより起こっているという考察を支持している。
SUS430鋼を用いた再溶解試験では、印加電流1000A以上で良好な再溶解が可能であること、印加電流の増加に伴って溶解速度が上昇する傾向があることを確認した。これらの結果は平成19年度に予備的に実施したSUS304鋼再溶解結果とほぼ同じであり、これら鋼種で溶解速度を変えて鋳塊を作成可能であることが判った。さらに高珪素SUS(SUS304ベース)を用いた再溶解試験を実施し、合金元素を添加した特殊鋼材でも問題なく再溶解が行えることを確認した。
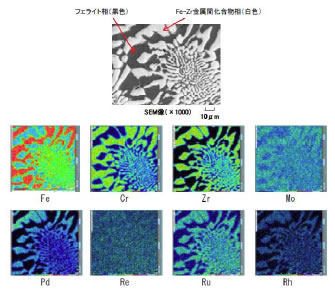
図5 溶解固化試料断面の元素分布測定結果
2.1.3 アクチニド除去後の陽極残留物の溶融固化試験
金属廃棄物の主成分となるフェライト系SUS(燃料被覆管)、Zr(陽極残留物)、一部の試験ではさらに模擬FP元素(Mo, Pd, Ru, Rh, Sb, Re)を秤量してY2O3をコーティングしたグラファイトるつぼに装荷し、誘導加熱により溶融させた。パラメータとして溶融温度/時間、装置内圧、Zr/SUS比、FP/(SUS+Zr)比などを変化させて得られる固化体性状への影響を調べた結果、Zr分布均一性の観点から溶融温度1700℃、溶融時間1時間、初期装置内圧41.3kPaが適当であることがわかった。固化体はフェライト(Fe-Cr)相と金属間化合物相が細かく入り組んだ微小構造を持っており、模擬FP元素のうちPd, Ru, Rhが金属間化合物相に多く分布し、MoとReは両相に分布した(図5)。
SUS-Zr-模擬FP合金溶融固化試験で作成された固化体について、廃棄物固化形態としての適用性を調べるために浸出試験を開始した。金属廃棄物はガラス固化体の様に粉砕することが困難なため、浸出試験は板状試料を用いるMCC-1法に則り、もっとも浸出量の多くなる条件(温度については90℃、浸出液pHついてはpH=4を純水の場合と比較)のみで試験を行った。また、金属廃棄体は使用済塩を固化したガラス結合ソーダライト固化体と共に廃棄されるため、これらのセラミックス固化体がすべて溶解したと仮定し、Cl濃度を1,000ppmとした溶液の試験も行った。浸出時間を70日と設定し、14日、28日後に浸出液をすべて取り替えることにより、固化体表面に形成されると予想される酸化保護層の影響を調べることにした。得られた浸出液の分析結果から各元素の規格化浸出量を求めたところ、これまでに報告されているガラス固化体に関する規格化浸出量に対して、2〜3桁以上も低い値であり、廃棄物固化体の性能として問題の無いものであることがわかった。
2.2 陰極析出物の処理技術開発
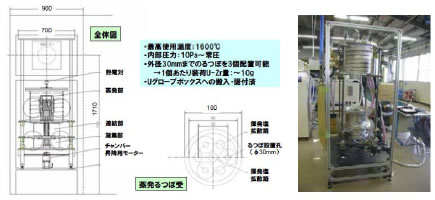
図6 U-Zr陰極回収物蒸留試験装置
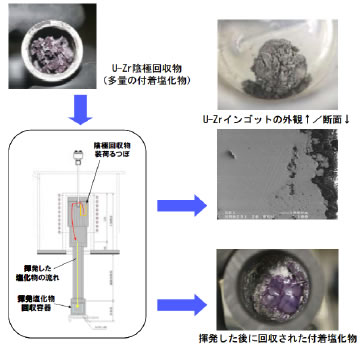
図7 高温蒸留による陰極回収物からの付着除去、U-Zrインゴット化
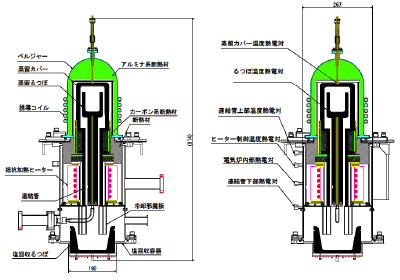
図8 工学規模蒸留装置主要部構造図
2.2.1 U-Zr陰極回収物の高温蒸留処理試験
本事業の中で平成19年度に製作したU-Zr陰極回収物蒸留試験装置(図6)について塩化物揮発時の閉じ込め性能を確認するとともに、陰極析出物付着塩を揮発除去するための運転条件を調べるために、最初に塩化物のみ(LiCl-KClあるいはLiCl-KCl-UCl3)を蒸発部に装荷して蒸留試験を実施した。最高1000℃で蒸留を行うことにより、塩化物を全て揮発除去することができた。また、揮発した塩化物の相当量が凝集部に到達する前に蒸発部/凝縮部間連結管内側等に付着したが、装置各部の重量増加分合計と装荷塩化物量との差は小さく、本装置における揮発塩化物のマスバランス(閉じ込め性能)が優れていることが確認できた。
続いて実際の電解精製試験で得られた固体陰極回収物を用いた蒸留試験を実施し、付着塩浴を除去すると共に、陰極析出物中のU-Zrの大半を塊として回収した(図7)。また、陰極回収物および溶融U-Zrを保持するるつぼ材料として、ZrO2コーティングを施したグラファイト、ZrO2またはZrO2/ZrN二層コーティングを施したタングステンが適用できる見込みを得た。
市販のZrO2コーティング材に含まれる焼結助剤が残らないコーティング層を作成するため、一度焼結させたZrO2層を粉砕して分級することにより得られた粒径約100μm以下のZrO2粒子を小粒径ZrO2のものにさまざまな割合で混合させて再度コーティングを行い、クラック発生が少なく機械的強度を保ったZrO2コーティング層を作成することに成功した。
2.2.2工学規模蒸留装置の開発
陰極処理装置内部温度分布の制御、製品および回収塩取出のための回収部構造の設計最適化、さらに陽極残留物の溶融固化と付着塩化物除去とを同時に行うことによる金属廃棄物処理合理化を目的として、本業務の中で平成19年度に製作した金属廃棄物溶融固化試験装置を、U換算で1kg/バッチ程度の工学規模蒸留試験装置として使用できるように改造を実施した(図8)。
本装置は内部圧力を13Pa(0.1Torr)程度まで減圧した上で蒸発るつぼ容器を最高1700℃まで加熱可能である。また、蒸発部から揮発した塩化物が途中で凝固して閉塞を起こさないように、回収部との間の連結部は抵抗加熱ヒーターにより1000℃まで加熱可能である。
空気雰囲気中での性能確認試験で、装置内部を仕様通り減圧できること、連結部温度と蒸発部温度をそれぞれ最高使用温度である1000℃/1700℃に昇温できること、加熱コイルや真空バウンダリーに加熱による不具合が生じないこと、KClを用いた蒸留試験において試験装置外部への揮発塩化物の著しい漏れがないことを確認した。最終的に本装置を既存の大型Ar雰囲気グローブボックス内に設置した後に昇温試験を実施し、蒸発部を固体陰極回収物および陽極溶解残留物からの付着塩除去とインゴット化に適した温度(最高1700℃)に保持し、揮発塩化物の凝固による連結部閉塞を起こさず、かつ回収るつぼを塩化物回収に適した温度に保つことができることを確認した。
3.今後の展望
(1)陽極残留物の処理技術開発
- 模擬合金を用いた試験によりESR法による不純物除去精製効果を評価する。
- 乾式再処理プロセスにおいて想定される幅広い金属廃棄物組成について、固化体の均一性や微視構造の観点から比較を行う。また、金属廃棄物固化体試料の組成が浸出挙動に及ぼす影響を調べ、上記の観察結果と合わせて適切な処理/組成条件を明らかにする。
(2)陰極析出物の処理技術開発
- Zr/U比が異なる陰極回収物を対象とした蒸留試験を実施し、乾式再処理工程管理のために十分なU/Zrインゴット回収物の均一性を実現するための条件を明らかにする。また、るつぼ材料として複数のセラミック及び複合素材を使用し、溶融U-Zr合金/塩化物との両立性を評価する。
- 工学規模蒸留装置を用いた試験により、固体陰極回収物のインゴット化と付着塩除去に適した装置設計・温度・圧力制御方法を提示する。
(3)陰極析出物/陽極残留物処理を含めた乾式再処理プロセスの構築
- 乾式再処理全体におけるアクチニド回収率を高く保持するために、本事業における試験結果をもとに、陰極析出物/陽極残留物処理で生じる回収塩化物を効率的に電解精製工程にリサイクルするためのプロセス設計を実施する。
4.参考文献
[1] M. Iizuka, K. Uozumi, T. Ogata, T. Omori and T. Tsukada, “Development of an innovative electrorefiner for high uranium recovery rate from metal fast reactor fuels”, J. Nucl. Sci. Technol., 46, 699.716 (2009).
[2] K. Uozumi, M. Iizuka, T. Kato, T. Inoue, O. Shirai, T. Iwai, Y. Arai, “Electrochemical behaviors of uranium and plutonium at simultaneous recoveries into liquid cadmium cathodes,” J. Nucl. Mater., 325, 34.43 (2004).
[3] T. Kato, T. Inoue, T. Iwai, Y. Arai, “Separation behaviors of actinides from rare-earths in molten salt electrorefining using saturated liquid cadmium cathode,” J. Nucl. Mater., 357, 105.114 (2006).
[4] D. Vaden, S. X. Li, B. R. Westphal, K. B. Davies, T. A. Johnson and D. M. Pace, "Engineering-scale liquid cadmium cathode experiments", Nucl. Technol., 162, p.124-128 (2008).