原子力システム 研究開発事業 成果報告会資料集
窒化チタンを不活性母材としたMA含有窒化物燃料製造技術に関する研究開発
(研究代表者)高野公秀 原子力基礎工学研究部門
1.研究開発の背景とねらい
本事業では、高速中性子炉を用いたマイナーアクチノイド(MA)分離変換技術の構築に寄与するために、熱的特性に優れる窒化チタン(TiN)を不活性母材とし、Pu及びAmからなる窒化物を分散させた(約50wt%)、非均質リサイクル用MA高含有窒化物燃料の製造技術開発を実施した。熱伝導率が高く燃料温度を低く保てることに加え、粒子分散型ペレットとすることで、核分裂片による照射損傷領域を粒子近傍に限定、アクチノイド元素再分布の抑制、FP保持性能向上等が見込まれ、一度の燃料装荷で効率的な核変換を目指した燃料概念である。
技術開発上の主要な課題は、1)Amが蒸気圧の高い元素であることから、焼結加熱中の蒸発損失を抑えつつ、所定の密度が得られる焼結条件を見いだすこと、2)(Pu,Am)Nで表される窒化物固溶体粒子をTiN母材に均質に分散させた上で、高い母材密度を達成することである。これらの基本条件をMAを模擬した希土類元素による試験で定めた上で、粒子径や含有率による製造性及び熱伝導率への影響を明らかにし、(Pu,Am)Nを用いた製造実証試験を実施した。
2.研究開発成果
2.1 希土類元素を用いた窒化物燃料ペレット製造技術の開発
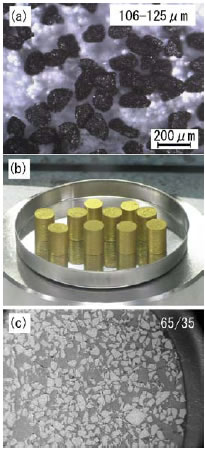
図1 (a) DyN粒子観察像
(b) DyN/TiNペレット外観
(c) ペレット断面観察像
H18年度には、不活性母材のTiN、及び燃料物質を模擬した希土類のDyNそれぞれについて、高密度化のための粉砕条件と有効な焼結助剤を実験により調べた。遊星型ボールミルを用いた粉砕条件の最適化の結果、TiNでは、Si3N4(窒化ケイ素)製の粉砕容器を用いることにより、窒素気流中1650℃、6時間程度の焼結加熱条件で、理論密度(TD)の90%を超える高純度な焼結体が得られることを明らかにした。一方、DyNの粉砕ではWC(炭化タングステン)あるいはZrO2(ジルコニア)製の容器が適することがわかったが、焼結助剤無添加では1600℃以下で85%TDの高純度な焼結体は得られなかった。種々の金属及び窒化物を焼結助剤として添加した結果、AlN(窒化アルミニウム)粉末を0.2から0.6wt%の範囲で添加した際に、最大で5%TD程度の焼結促進効果があることを見いだし、85%TDの密度を有するDyNが得られる条件を確立した。助剤添加による熱伝導率への影響を調べた結果、DyNにAlNを0.5wt%添加しても熱伝導率の低下は見られなかった。
H19年度には、DyN焼結体をローターミルで破砕して粒子状とし(図1(a))、TiN微粉末と混合・成型したものを1650℃で焼結することにより(図1(b))、燃料ペレットの製造技術開発を実施した。混合には、無水ヘプタンを分散媒とし、超音波による振動を用いた湿式混合法を採用することにより、均質分散性を向上させた(図1(c))。DyN含有率(10、20、30、35mol%)、及び粒子径(<63、63-106、106-180、180-250μm)をパラメータとして製造性への影響を調べた結果、1)TiN母材密度は粒子含有率増加に対して直線的に低下すること、2)焼結後のペレット形状は粒子径が大きい程樽型に歪む傾向が見られたことにより、粒子含有率20mol%強まで、粒子径63-180μm程度が現実的な範囲であるとの結論を得た。なお、粒子のエッジ部分が母材収縮時の妨げになっていると考えられ、これを丸めるよう改善することで母材密度をさらに高めることが課題である。
燃料ペレットを切断して得たディスク状試料について、軸方向の熱伝導率を測定した結果、DyN含有率増加に伴い熱伝導率が低下するだけでなく、粒子径増大に対しても低下することがわかった。したがって熱伝導率の観点からも粒子径は小さいほうが好ましいことを明らかにした。
窒化物の熱伝導では電子の寄与が重要な役割を果たすため、TiN、DyN及び燃料ペレットそれぞれについて径方向の電気伝導率を測定し、その寄与を明らかにした。電子及びフォノンの寄与から評価したペレット径方向の全熱伝導率は、軸方向実測値の約1.3倍となり、ペレット成型時に粒子の長軸が径方向に配向した効果が示唆される。
2.2 MA含有窒化物燃料ペレットの製造実証試験
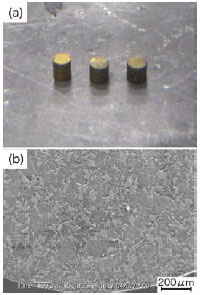
図2 (a)(Pu,Am)N/TiNペレット外観、(b)同ペレット断面観察像
Amを用いた試験では取り扱える試料量が制限されるため、H19年度には微少量試料を想定したコールド試験をAm取り扱い用グローブボックス及びホットセルで実施し、機器の性能・操作性を確認するとともに一連の試験手順を定めた。
H20年度には、まず酸化物から炭素熱還元法によりPuN、AmN、(Pu0.75Am0.25)Nを調製し、微粉砕後、それぞれの焼結体を作製した。(Pu,Am)N焼結体では、Amの蒸発損失を十分低く(0.14-0.27wt%)抑えた上で、85%TD以上の密度が得られることを実証した。次に、PuN及び(Pu,Am)N焼結体を破砕して粒子を作製し(<63μm、63-150μm)、粒子含有率20mol%(50wt%)でTiN粉末と湿式混合後、窒化物燃料ペレットを焼結した(図2)。母材相対密度は最大で80%TD程度であり、同じ粒子含有率のDyN/TiNペレット(85-87%TD)に比べて低かった。この原因を検討した結果、微少量化のための破砕形式の違いによる粒子形状悪化(エッジ形状増加)と、湿式混合時のヘプタン残留が複合的に影響していることを明らかにし、今後改善すべき課題とした。図3に軸方向熱伝導率の評価結果を示すように、(Pu,Am)N/TiN燃料ペレットの熱伝導率は、1000℃で最大15 W/mKであったが、実燃料で想定される粒子含有率(20-25mol%)では、上記の改善を施すことにより、20 W/mK程度まで向上可能な見通しを得た。
一方、PuN、AmN及び(Pu,Am)Nの電気伝導率を取得し、図4に示す通り気孔率への依存性を整理した結果、固溶体の電気伝導率は成分窒化物の実測値から線形混合則で近似できることを見出した。(Pu,Am)N/TiNペレット径方向の電気伝導率測定結果から、径方向の全熱伝導率は軸方向実測値の1.3倍程度と評価され、DyN/TiNペレットの場合と同様に粒子長軸の配向効果が示唆された。
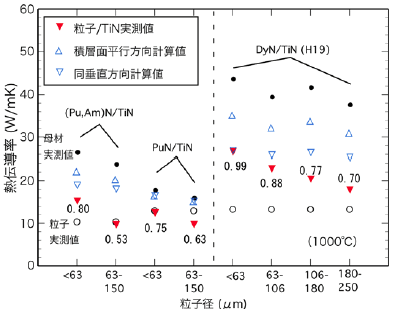
図3 熱伝導率実測値と積層モデル計算値との比較
(記号下数値は垂直方向計算値に対する実測値の比)
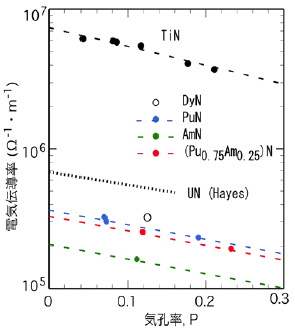
図4 電気伝導率の気孔率依存性
3.今後の展望
粒子形状改善による母材密度向上と、それに伴う熱伝導率向上の課題に取り組みつつ、照射試験用ペレット製造を視野に入れた製造規模拡大の具体的検討を進めるとともに、熱膨張率や熱機械特性等の物性データ取得を進め、それらからの粒子径への要求を検討する。