原子力システム 研究開発事業 成果報告会資料集
ガス冷却高速炉用高燃焼度燃料の開発
(研究代表者) 檜木達也 エネルギー理工学研究所 准教授
(再委託先) 独立行政法人日本原子力研究開発機構
1.研究開発の背景とねらい
ヘリウムガス冷却炉心において、熱効率を40%以上とするために、冷却材のホットスポットでは最高1000℃程度になると予想され、熱伝導率に優れた窒化物燃料が候補となっている。高速増殖炉サイクルの実用化戦略調査研究(FS)では、高燃焼を達成するためには、窒化物燃料を50%程度含み、固相マトリックスを高密度SiCで形成する概念が有力とされている。しかしながら、窒化物燃料を均一に分散させ、マトリックスとして95%を超えるような高密度SiCを形成させるような技術は存在しない。京都大学で開発したSiC/SiC複合材料の作製技術を応用することにより、高密度で高純度のSiC固相マトリックスを持つ、高燃焼度窒化物燃料開発のための基本技術を得ることを目的とした。新たな作製方法として(図1)、脱炭処理により穴のある高密度SiCを形成し、その穴に棒状の窒化物燃料、バッファ相を形成するという全く新しい手法を導入した技術開発を行い、熱効率40%以上の高い経済性を有するガス冷却高速炉実現のために不可欠な、高性能な高燃焼度窒化物燃料のシンプルな作製技術を開発する。燃料要素設計、プロセス・燃料要素開発、材料特性評価、再処理技術の開発を行い、燃料密度約50%の緻密なコンポジット燃料の基本的な作製技術を確立する。
図1 本研究におけるコンポジット燃料作製の流れ
2.研究開発成果
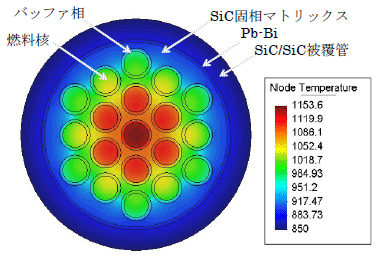
図2 本事業で得られた物性を考慮した燃料の熱計算結果
(燃料核径1.2 mmφ)
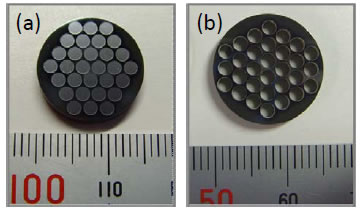
図3 30個の炭素棒及び円柱状貫通孔を有する
SiC固相マトリックス
((a):脱炭処理前、(b):脱炭処理後)
固相マトリックス及びバッファ相を、1000℃を超える高温クリープ特性を含む強度特性、走査形電子顕微鏡、透過形電子顕微鏡等による微細組織の評価結果に基づき、原料粉末、焼結助材、温度、圧力等の作製条件を制御した最適化を行い、基本的な目標の条件を満たす理論密度の95%以上の固相マトリックス、50%以下のバッファ相の作製に成功した。
固相マトリックス及びバッファ相の強度特性及び熱特性の実際の物性値、FSから得られた高燃焼窒化物燃料の概念と、文献調査から得られる燃料特性等から、燃料要素設計を行った。実環境を考慮し、高燃焼度においても健全なコンポジット燃料の作製方針を検討するために、核分裂生成(FP)ガスに起因した内圧に対する固相マトリックスの健全性を評価し、設計が成立する基本的な燃料仕様として、燃料核径、バッファ相厚さおよび燃料間寸法の関係を把握した。解析は、燃料核を19個有するコンポジット燃料を対象として、FPガスによる固相マトリックス内の応力分布、さらにはSiC/SiC複合材料被覆管や液体金属ボンドも含めた熱計算によりコンポジット燃料内の温度分布を求めた。これより本事業で開発した固相マトリックスの強度評価結果を取り入れた燃料要素設計を実施し、要求される燃料核径、燃料間寸法及びバッファ相厚さを示した。本事業で取得した強度、熱等の材料特性、非常に薄い燃料間距離を達成する作製技術を取り入れた燃料要素設計により、燃料温度は図2に示すように、当初設定していた1600℃(高速増殖炉サイクルの実用化戦略調査研究における設計制限温度)よりも低くなることが分かり、これによりバッファ相厚さを低減し、燃料体積密度を高く設定することが可能となった。この際の、固相マトリックスの最高温度は1092℃であり、固相マトリックスのクリープ特性からも十分に健全であることが示され、当初設定した燃料密度を達成し、尚且つ高燃焼度においても健全な燃料形態を得た。これらの計算結果より、本事業における作製技術目標として、燃料間距離0.23mm以下、バッファ相厚さ0.15mm以上を設定した。
脱炭処理に用いる炭素棒の熱膨張係数等の特性の検討、冶具等の開発により、炭素棒の周りのSiC原料に均一に圧力をかけ焼結させる技術の確立等により、図3に示すように、15mm径の中に30個の穴を持つ固相マトリックスの作製に成功した。この燃料及びバッファ相用の穴間距離約0.20mmで、燃料要素設計から得られた目標を満たす。さらに、模擬燃料バッファ相原料を入れ、無加圧焼結することにより、最終目的とするコンポジット燃料の技術開発に成功した。本技術は脆性材料のセラミックスの微細加工技術としても、汎用性の高い技術である。高速増殖炉サイクルの実用化戦略調査研究フェーズIIで最も有望な概念とされた六角ブロック型燃料集合体に関しては、従来、製造技術に課題があったが、本事業で開発した方法を用いることにより、課題を克服できることが示された。
再処理性に関しては、既存技術の応用として、湿式法で用いられる硝酸に、最終条件で作製した固相SiCマトリックスの浸漬試験を行い、固相SiCマトリックスの安定性を示すとともに、再利用の可能性も示した。
3.今後の展望
高速増殖炉サイクルの実用化戦略調査研究フェーズIIにおいて、ヘリウムガス冷却炉は、ナトリウム冷却炉に次ぐ概念とされたが、技術的な課題として、燃料集合体が第一に挙がっており、本事業の成果は、ヘリウムガス冷却炉の最大の課題に対する実現性の可能性を広げるのに十分に貢献したものと考えられる。本事業における材料特性の評価は、非照射材でのみ行っているため、照射材を用いた評価は今後必須である。近年の研究において、高結晶性、高純度のSiCに関する高温照射下での安定性は示されつつあり、本業務で開発したSiCもこれらの要件を満たす材料であるため、高温照射下での実環境下においても、健全であることが期待されるが、照射データが無いため想定される環境での照射実験が必要である。燃料被覆管や冷却管の候補とされるSiC/SiC複合材料に関しては、管材等の製作性も近年著しく向上しており、フェーズIIの前提条件も大きく変化していることから、ヘリウムガス冷却炉の開発研究に対する更なる適用研究が今後大いに期待される。今後、実用化に向けては、実コンポジット燃料を含む耐照射特性試験と評価、固相SiCマトリックスと液体金属ボンドとの共存性評価、燃料の製造性も考慮した燃料被覆管を含む燃料体の開発、燃料および燃料体の遠隔製造技術の開発が必須となる。