
原子力システム 研究開発事業 成果報告会資料集
ガス冷却高速炉用高燃焼度燃料の開発
(受託者)国立大学法人京都大学
(研究代表者) 檜木達也 エネルギー理工学研究所 准教授
(再委託先)独立行政法人日本原子力研究開発機構
(研究代表者) 檜木達也 エネルギー理工学研究所 准教授
(再委託先)独立行政法人日本原子力研究開発機構
1.研究開発の背景とねらい
ヘリウムガス冷却炉心において、熱効率を40%以上とするために、ホットスポットでは最高1000℃程度になると予想され、酸化物燃料および窒化物燃料が候補となっている。高速増殖炉サイクルの実用化戦略調査研究(FS)では、窒化物燃料を用いて高燃焼を達成するためには、窒化物燃料を50%程度含み、固相マトリックスに高密度のSiCで形成される概念が有力とされている。しかしながら、窒化物燃料を均一に分散させ、マトリックスとして95%を超えるような高密度のSiCを形成させるような技術は存在しない。京都大学で開発したSiC/SiC複合材料の作製技術を応用することにより、高密度で高純度のSiC固相マトリックスを持つ、高燃焼度窒化物燃料開発のための基本技術を得ることが目的である。新たな作製方法として、脱炭処理により穴のある高密度SiCを形成し、その穴に棒状の窒化物燃料、バッファ相を形成する技術開発を行う。熱効率40%以上の高い経済性を有するガス冷却高速炉実現のために不可欠な、高燃焼度燃料の作製技術開発を目的とする。図1に示すように、高密度なSiCを形成する技術を基本として脱炭処理により、棒状の穴をあらかじめ作製し棒状の模擬窒化物燃料を挿入し、バッファ相を形成するという全く新しい手法を導入することにより、シンプルで高性能な窒化物燃料の作製技術開発を行う。燃料要素設計、プロセス・燃料要素開発、材料特性評価、再処理技術の開発を行い、燃料密度約50%の緻密なコンポジット燃料の基本的な作製技術を確立する。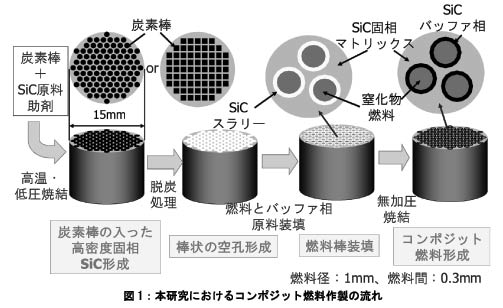
2.研究開発成果
燃料要素設計に対して、実環境下で想定される応力、本研究で作製した材料の物性値から、棒状の燃料間距離、バッファ相厚さの合理的な設計値の検討を行った。FSにおけるPu富化度(内側16.5 wt.%/外側22.8 wt.%)と同程度のPu富化度にて炉心性能を担保するために、燃料間距離100〜300μmでの窒化物燃料要素の分散制御技術を開発し、燃料製造の成立性を実証することを試みた。バッファ相は、核分裂生成(FP)ガス等の保持、燃料核スウェリングの吸収、核燃料元素移動の緩衝という役割があり、ガスプレナム長を短縮した本概念においては非常に重要な役割を果たす。燃料の照射挙動を考慮し、想定される燃焼度において安全性を有する燃料のバッファ相厚さについて検討を行った。照射によるFPガスのバッファ相内における内圧を計算し、この内圧によって生じる応力が固相マトリックスの許容応力よりも小さくなるようにバッファ相厚さを設定した。計算で用いた固相マトリックス許容応力やバッファ相の密度等は、本研究で作製した試料から実際に評価した物性値を用いた。一次元モデルでの計算結果においては、最適値として、燃料径1.2mm、バッファ相厚さ420μmという値が導き出された。TiN、ZrNを本研究で用いる模擬窒化物燃料として検討を行った。バッファ相を含む構成要素の基本物性の整備、コンポジット燃料製造技術統合の結果や熱応力計算の結果も考慮し、実験で得られた熱特性が実際の燃料の文献値と近いZrNを中心に、基本的な開発を進めることとした。プロセス・燃料要素開発として、炭素棒を含む高密度SiCを形成するための原料粉末の選定、焼成条件、圧力のかけ方などの検討を行った。炭素棒に対して垂直に圧力をかけた場合、炭素棒横に助剤の偏析が生じたが、炭素棒を圧力方向に配置し、周りのSiC原料に均一に圧力をかけ炭素棒周りの低加圧領域を削減し焼結させる技術開発を行い助剤の偏析を抑制した。原料SiC粉末の選定とブレンド、助剤の最適化により助剤の偏析や炭素棒界面との反応層を抑制した高密度SiCの形成を行い、炭素棒を含む固相SiCマトリックスの作製に成功した。脱炭プロセスに用いる炭素棒の種類、雰囲気、温度の条件の最適化を行い、制御した穴を持つ固相SiCマトリックスの形成に成功した。炭素棒や穴の周りに焼結助剤の偏析や亀裂などは観察できず、固相SiCマトリックスに奇麗に穴が形成された。本研究で作製された固相SiCマトリックスの密度は当初の目的である理論密度の95%を達成している。これらの結果から本事業で最終的に目標とする燃料密度約50%という緻密な成形技術に目処が立った。この方法は、SiCのように非常に硬く、脆いセラミックスの加工法の開発としても、機械加工のように試料にダメージを及ぼす可能性が無いため、本研究で目指すような多量の穴を100μmオーダーの距離で加工することが可能であることを示しており、加工技術としても重要な成果である。
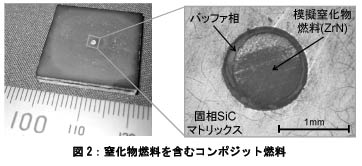
本研究で作製した固相マトリックス、バッファ相のSiCに対しては、1000℃以上の高温を含む強度特性、熱特性の評価を実施し、得られた試料の物性値は燃料要素設計に反映した。
3.今後の展望
被覆粒子タイプでは、高密度を達成するだけでも困難で、粒子の配置を制御することはできない。本方法では、棒状であり、高密度を得やすいのと、穴の径、位置の制御も可能である。被覆粒子タイプを含む同様な概念では、燃料とその隙間にマトリックスの原料を入れて、加圧焼結するため、燃料や被覆粒子に損傷が生じる可能性があるが、本方法では、固相マトリックスを先に作製し、最終的に無加圧焼結で燃料自身に圧力を加えることなく、バッファ相を形成するため、燃料自身の健全性が保たれやすい。再処理の点でも棒状を採用しているため、非常に有利である。本研究では、比較的汎用性の高い技術開発ではあるが、研究室レベルでの段階である。照射下での挙動の評価を実際に行っていないため、実機へ向けた課題としては、固相SiCマトリックス、模擬コンポジット燃料の耐照射特性試験と評価、固相SiCマトリックスと液体金属ボンドとの共存性評価、実燃料を用いたコンポジット燃料の耐照射特性試験と評価を行うことが必要である。これらに加え、被覆管を含めた総合的な燃料体の開発、燃料の遠隔製造技術開発等の開発により、最終的に実機への適用の目処が立つものと考えられる。これらの基本技術は他の概念の燃料への応用も期待される。